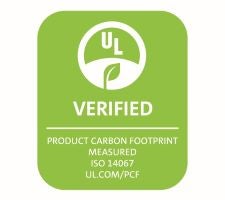
Demand for product carbon footprints is growing
An increasing number of companies are measuring and reducing their products’ carbon footprint due to pressure from outside influences, including:
-
Retailers and supply chain1
Companies purchasing materials, components and finished products expect suppliers to disclose product carbon emissions data. -
Consumers2
Products with a sustainable label are seeing faster growth than their conventional counterparts. -
Regulators3
Jurisdictions around the world, including in the EU and the U.S., have introduced requirements aimed at lowering carbon emissions. -
Investors4
Financial institutions are considering environmental, social and governance (ESG) practices, including climate change mitigation, in investment decisions and expect investees to disclose high-quality data.
Why a product carbon footprint should be verified
Measuring the carbon footprint of products following ISO 14067 shows stakeholders your dedication to climate protection and enables you to set targets and create a carbon reduction pathway for your products. Creating a product carbon footprint (PCF) is often a time-consuming, complex process, and data errors are not uncommon. Verification helps demonstrate the reliability, consistency and accuracy of your carbon footprint and supporting information by confirming whether your greenhouse gas statement meets international standards. For manufacturers who not only have measured their products’ footprint but also have taken steps to reduce it, verification provides credibility to the claimed reduction and helps prevent greenwashing by providing evidence of genuine efforts toward reducing environmental impact.
UL Solutions verification services
A PCF verification measures the greenhouse gas emissions of a product throughout its entire life cycle from material procurement through end of life. Manufacturers must first create a life cycle assessment (LCA) following ISO 14040 and ISO 14044, which forms the basis for the PCF report. When carbon reduction is assessed, a comparative study of the old and new version of the product is additionally required.
UL Solutions offers multiple PCF verification options to suit a variety of customer needs. Consult the table below to determine which verification program is most suitable for your product:
Criteria | Carbon measured program | ISO 14064-3 carbon footprint verification program* | Carbon reduced |
---|---|---|---|
Standard compliance | ISO 14067 | ISO 14067, verification following ISO 14064-3 | ISO 14067** |
Site visit | No | Typically yes | No** |
Life cycle assessment required for verification | Yes | Yes | Yes – Comparative study required of new vs. old product version |
Process | Confirms compliance to standard and program criteria through critical review of LCA and PCF | In addition to compliance with criteria, we also conduct a risk-based approach that evaluates the truthfulness of the PCF report and primary data used | Follows carbon measured process, confirming comparison criteria and minimum reduction is met for comparative study** |
Deliverables | Product carbon footprint measured statement of verification | Product carbon footprint statement of verification to the limited or reasonable level of assurance | Product carbon footprint reduced statement of verification |
Risk mitigation level | Medium Suitable for those that wish to show ISO 14067 standard compliance |
High May be necessary for financial disclosures or to comply with specific PCF frameworks |
Medium** Suitable for those that wish to show ISO 14067 standard compliance |
* The extent of verification to ISO 14064-3 differs by two levels:
- Reasonable – Where the nature and extent of the verification activities have been designed to provide a high — but not absolute — level of assurance of historical data and information.
- Limited – Where the nature and extent of the verification activities have been designed to provide a reduced level of assurance of historical data and information.
** The ISO 14064-3 verification approach can optionally be used for the carbon reduced program when a higher level of risk mitigation is needed. A site visit may be required.
Working with UL Solutions for product carbon footprint verification
By working with UL Solutions to verify your product’s carbon footprint, you can leverage our trusted brand, reduce the risk of carbon calculation data errors, and build a high level of confidence with interested parties that your greenhouse gas (GHG) statements are materially correct and meet international standards. Companies who utilize our PCF reduced verification service can additionally gain credibility and recognition for their efforts in mitigating climate change.
With the completion of your product carbon footprint verification, you are provided with the applicable UL Verified Product Carbon Footprint Mark. This Mark is your tool to promote your achievement and the highlight the steps you are taking on your product sustainability journey and continuous improvement.
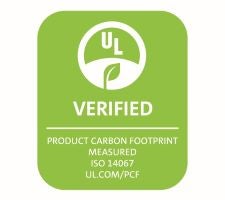
Watch now: Greenhouse gas verification
UL Solutions offers independent verification of enterprise and product GHG statements to ISO 14064-3, the international standard for verification of GHG claims.

Product Carbon Footprint Services
Get connected with our sales team
Thanks for your interest in our products and services. Let's collect some information so we can connect you with the right person.