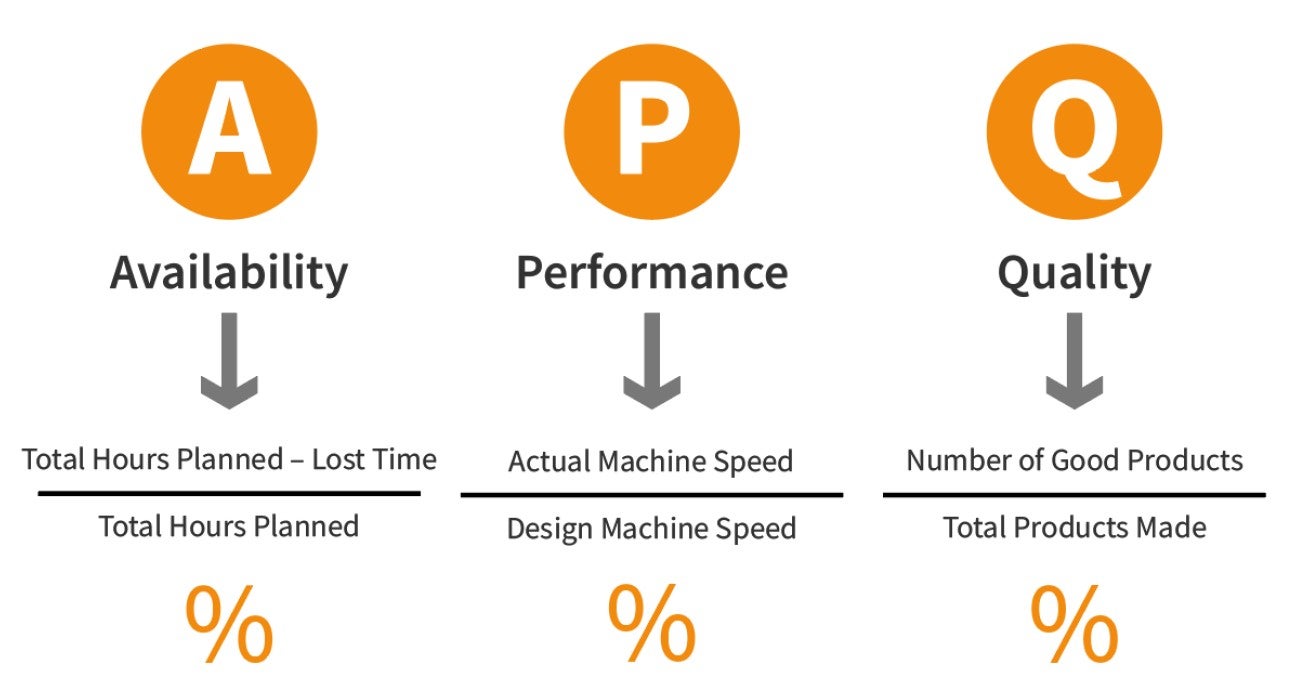
The asset value of the machines that make up a typical wire and cable plant can be in the tens of millions of dollars/euros. These assets can operate for many years and are often repurposed as designs change, and the manufacturing mix evolves.
When sales volumes increase in a facility assumed to be operating at capacity, additional hours are typically worked, either as overtime or extra shifts. While this approach works assets harder and has a positive, albeit incremental, impact on short-term financial performance, it does not improve productivity.
When issues that affect overall equipment effectiveness (OEE) remain unaddressed and standards slip, productivity has a habit of drifting lower or never fully reaching the levels predicted when the assets were initially specified.
This article considers best practices for the entire lifecycle of an asset, from specification to retirement. It describes the use of OEE as the measure of productivity for assets. It describes the impact that supporting functions can have on an asset’s productivity; technical, process engineering, maintenance, planning, and production management.
This article examines:
- Impact of planning on OEE.
- Impact of maintenance on OEE.
- Impact of process engineering on OEE.
- Impact of production management, supervisors & operators on OEE.
- Effective ways to measure and record OEE.
- Setting OEE targets.
- How technology can help improve OEE in wire and cable manufacturing.
What is overall equipment effectiveness?
Overall equipment effectiveness (OEE) is calculated as a percentage that effectively reflects how much saleable or useable product is produced by an asset, a group of assets or a whole factory in a specific time period. It is the product of three ratios: availability, performance, and quality.
- Availability – Measures the time spent producing a good quality product during a specific period. A Nett and Gross can be calculated. Nett is the time spent making a good quality product versus the total time an asset is planned to run, which may be only one or two shifts a day. Gross can consider the 120 hours Monday to Friday or 168 hours of 7 days.
- Performance – Compares the actual output in a time period to that which was planned to be produced, termed Nett Rate, or to the theoretical design rate of the asset, termed Gross Rate. Businesses often run assets below the top limit due to process variations affecting quality or an underdeveloped process engineering effort. Therefore, a business must understand the difference between Nett and Gross and seek to close it over time.
- Quality – Measures the total length of good product made versus the full length manufactured — the difference typically being scrap.
Using the above definitions, Nett OEE can measure the effectiveness of the production function to produce to an agreed standard. Gross OEE becomes a more strategic or mid-term tactical measure to show the headroom to full theoretical capacity. This can be useful when considering new contracts, peak periods, and engineering improvements. Nett OEE would usually be embedded in a business’s planning and costing systems as the basis of its standards.
See this equation:
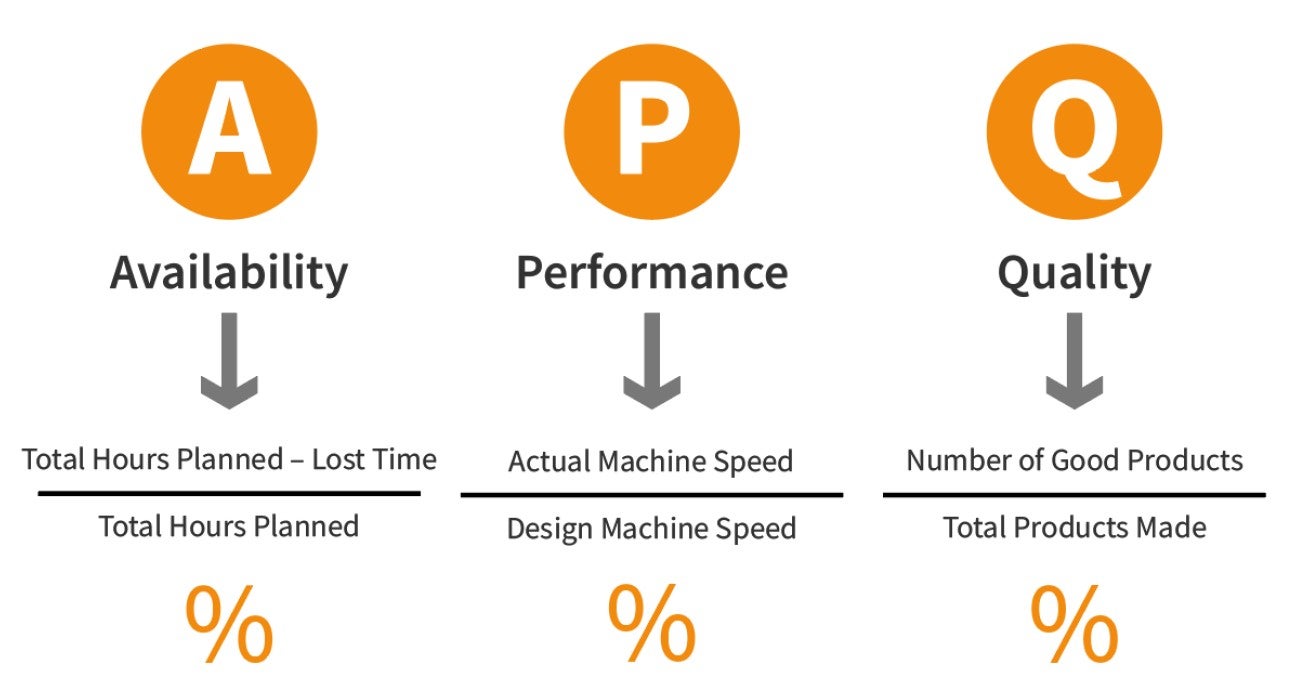
Factors impacting OEE
Impact of planning on OEE
The systems used by the Planning Department to plan and schedule production should use the proven Nett OEE figures established for production. Based on trends, the Nett OEE being applied can be positively and negatively updated. Using incorrect values can lead to over-planning, potentially impacting customer service or stock levels, or under-planning, where machines may be waiting for work, and labor could be idle.
The timing and sequencing of changeovers are significant factors when considering the potential impact of planning on efficiency. For example, scheduling lighter-colored polymers ahead of dark ones is good practice to speed up color changes. In addition, a good understanding of wire-drawing strings and how changes, such as wire size, should be optimized is vital.
Also, scheduling stranding, lay-up and armoring in a manner that reduces the number of drum changes is critical for minimizing downtime.
Planning, and finite scheduling, can be undertaken using sophisticated scheduling software, but it is also possible to provide production management with the flexibility to sequence its operations to maximize efficiency. When planning is being conducted using an integrated manufacturing execution system (MES), the business-wide communication of the schedule can be easily communicated.
Impact of maintenance on OEE
Factories that experience a high level of unscheduled downtime due to breakdowns are inherently inefficient, and the impact of a breakdown in one area can cascade through a plant. These unscheduled events often lead to extended downtime while waiting for external technical specialists and spare parts.
An effectively planned maintenance regime based on time or frequency and appropriate predictive techniques is a fundamental requirement for a capitally-intensive cable factory. Typically, unplanned downtime should be less than 3% of total machine hours and up to 5% of planned maintenance.
As well as downtime, poor maintenance can lead to rate losses and poor quality. A poorly maintained machine may be temporarily or permanently down-rated for speed — this would be adjusted in the Nett OEE for planning purposes but would show deterioration in Gross OEE. Examples are a worn screw in an extruder, tension control in wiredrawing and insulation, or limiting the rotation speed of large drums at lay-up or sheathing.
A timely response by maintenance to requests from production to attend to a machine is also essential in maintaining asset productivity. Waiting for maintenance should not be a principal reason for reduced OEEs.
Impact of process engineering on OEE
Process engineering should be involved in the specification process of any new assets. The target speeds, planned changeover times, and inherent scrap should be understood before acquiring an asset and embedded in the contract for its purchase. The Factory Acceptance Test (FAT) and Site Acceptance Test (SAT) should only conclude when the target productivity levels have been achieved.
Too often, assets are rushed into production and not thoroughly tested and optimized. It can take several weeks to achieve targeted performance levels, but this should be done, and the assets should then be formally handed over to production. Standards for each product to be manufactured should be defined and recorded in the site’s systems and standards. These will form the basis of the Nett OEEs.
When the production function reports a process engineering issue leading to scrap or a slow-running process, engineering should quickly correct the problem.
Impact of production management, supervisors and operators on OEE
The production function truly holds the key to achieving the planned OEE performance. Directly by the actions of process operators, speeds are set, changeovers are affected efficiently, and scrap is kept low. Good, diligent operation of machinery is the fundamental duty of production operators. Supervisors should make regular and frequent assessments throughout a shift and complete the preparation for changeovers.
“Waiting for materials,” “waiting for instructions,” “waiting for tooling,” or “waiting for job” are categories of downtime that supervisors have a role in minimizing. Ensuring that machines are being operated at planned speeds by operators throughout a production run requires diligence from supervisors. Actions must be taken proactively and quickly to keep OEE at target levels.
When variances in rate, availability, or quality occur, supervisors should be aware of them. They should explain performance at the end of a shift for the area under their control and be proactive in following up on any actions requiring support from other functions. Supervisors should make operators aware of their individual and collective performance and the impact that any variances have had on efficiency and potentially on customer service and cost.
Production management typically reviews the performance of the previous day’s shifts as the first task of a new day. Any unresolved issues carried into the current day should form their immediate focus.
Every month, a review led by production and involving process engineering, maintenance, and planning should review OEE and develop any corrective actions needed to address the evident main losses.
Measurement and recording of OEE
There are several ways to gather data that facilitate the calculation of OEEs, such as:
- Line-side whiteboards can track output versus plan, downtime, and scrap. OEE can be calculated manually at the end of a shift. This has the benefit of visibility and ownership. It can distract an operator’s attention and, when there are issues, can be inaccurate as time passes before the recording starts. It is also not available widely to the business.
- Short-interval control sheets, typically A3 pre-formatted sheets, can be completed by operators during a shift with data recorded at predetermined intervals, e.g., 15-minute blocks. These can be analyzed by the operator or supervisor at the end of a shift and entered into a production office database by an administrative resource. This has the benefit of recording the data digitally, facilitating automatic analysis and trending.
- Computers can gather data directly from the production lines, and operators can enter stop codes to indicate why their machines are not running. If machines have to run slower than planned, computers enable the creation of online notes and the ability to enter scrap data. These computers may be standalone or linked to a central point; they may also compare actual versus planned performance. OEEs can be calculated and displayed in real time, and alarms can be set up to improve awareness and prompt action.
Measurement and recording are only useful, however, if they prompt action. Production management, supervisors, and the daily operators bear the most significant responsibility for these actions.
What OEE targets should be set?
OEE targets depend on many factors, not least the nature of the cables being manufactured. If a narrow range of cables manufactured using common sub-elements is produced, changeovers should be minimal and predictable. If a five-day, 24-hour operation is deployed, there is only one cold start.
If a seven-day, 24-hour operation is the norm, there are potentially no cold starts. A target Nett OEE in the 90%-95% would be expected in these environments. It is also likely that the gap between Nett and Gross OEE will be narrow as a lack of variety of production facilitates optimization.
In factories where a wider range of to-be-made orders is the norm, lower Nett OEEs may be appropriate as changeovers will be more frequent and complex, and rates may be increased during a run once it is clear that quality is under control. The worst thing a cable factory can do is compromise quality for efficiency, as a scrapped length of high-value cable can often wipe out the benefits of trying to run fast. It is also likely that the gap between Nett and Gross OEE will be wider in these environments.
OEEs can be set for individual machines, groups of machines, production cells, and critical paths or bottleneck routes. In the case of factories with bottlenecks, a high OEE for the whole factory can mask a core problem if the OEE of the backup is well below target. The output will be limited, and customer service may be poor, yet OEE may look good overall. Using OEE wisely and as part of a basket of KPIs in a balanced scorecard is vital.
Can technology help improve OEE?
Asset efficiency is crucial for competitiveness in asset-intensive industries and process manufacturing. Although 85% of manufacturers recognize the role of digital technologies and the potential of Industry 4.0 in increasing asset efficiency, only 15% of companies have dedicated strategies for enhancing asset efficiency. This represents a great deal of inefficiency, and opportunity, in the overall manufacturing process.
A digital strategy encompassing cable and process design, Material Requirements Planning (MRP)3, scheduling, and manufacturing execution ensures that the critical process and product data used for managing the business are used consistently throughout the company and that any variances are recorded and visible.
Performance improvement programs that can gain vital real-time information to enhance performance can boost operational efficiency by up to 25%. This can transform the financial performance of a cable factory.
A solution to automatically capture OEE
CableMES has been developed specifically for wire and cable manufacturers. It closes the loop between the high-level business and low-level plant and process functionalities.
CableMES sits between the business systems, i.e., enterprise resource planning (ERP), and the plant systems, i.e., supervisory control and data acquisition (SCADA) and process control providing the most efficient and cost-effective operational and production environment possible.
CableMES provides all the tools required to automatically capture OEE and its underlying components so that the shop floor team can react immediately to any production performance issue in their area. The process improvement team can look for past trends to make process improvements.
CableMES automates the collection of the three elements of OEE analysis (availability, performance, and quality), reducing paperwork and data entry.
- For quality, CableMES (through its integration with cable design software CableBuilder Enterprise) ensures that quality plans and product/machine tolerances are defined for every production run.
CableMES (through its integration with Aveva System Platform, formerly known as Wonderware) records the actual process values that affect quality. It can therefore determine the length of cable that is good quality versus bad quality.
The Quality element of OEE can be automatically calculated for every production run for every machine. This means a sub-standard product is identified immediately, and remedial action can be taken. Furthermore, a bad product is automatically quarantined, blocking its movement to the following process, so no further value (and costs) will be added. - For performance, CableMES records the target line speed for each production run and can calculate the average actual line speed for each production run. The Performance element of OEE can therefore be calculated for every production run for every machine. This means that a slow-running machine is identified immediately, and remedial action can be taken.
- For availability, CableMES records the running status of each machine. The Availability element of OEE can therefore be calculated for every production run for every machine. This means that a stopped machine is identified immediately, and remedial action can be taken.
Conclusion
Measuring OEE maximizes asset productivity
Measuring the productivity of assets within wire and cable manufacturing is vital. Calculated as a percentage that reflects how much saleable or useable product is produced by an asset, a group of assets, or a whole factory in a specific time period, OEE allows for benchmarking and process improvement plans to be created.
When issues that affect OEE remain unaddressed, and standards slip, productivity has a habit of drifting lower or never fully reaching the levels predicted when the assets were initially specified.
Every function of the shop floor must work together to maximize productivity
Examining production workflow is vital. The ability to identify pain points and bottlenecks, conduct an analysis of the people carrying out various roles on the shop floor and undertake continuous assessments of the technology and machinery in the workflow helps identify areas for improvement.
Move from manual to digital capture of OEE data
Digitalization is changing the landscape of manufacturing. Monitoring production processes and capturing real time, robust data enables OEE to be calculated with speed and accuracy. Reliance on manual processes and human data input exposes the whole business to unnecessary risk. For example, a one-digit error on a calculation can cascade through the entire shop floor and result in miscalculations across many other functions.
Smart factory solutions ensure accurate OEE calculations
The transition to smart factory status and the integration of software to streamline the entire production workflow can be easily achieved when partnering with an established all-encompassing solutions provider. Regardless of company size and budget, dedicated software programs can be installed to maximize productivity and profitability, such as CableMES, which ensures automatic and accurate OEE calculations.
Key takeaways
- Effectively manage the timing and sequencing of changeovers, e.g., schedule lighter-colored polymers ahead of dark to speed up color changes.
- Use robust scheduling to minimize downtime, e.g., scheduling stranding lay-up and armoring in a manner that reduces the number of drum changes is critical for minimizing downtime.
- Install an integrated manufacturing execution system (MES) to enable the business-wide communication of the schedule and automatically capture OEE.
- Create an effective maintenance regime based on time or frequency coupled with appropriate predictive techniques.
- Establish a robust reactive maintenance procedure – waiting for maintenance should not be a principal reason for reduced OEE.
- Set targets for speeds, planned changeover times, and inherent scrap before acquiring an asset.
- Factory Acceptance Tests (FAT) and Site Acceptance Tests (SAT) should only conclude when the target productivity levels have been achieved.
- Do not rush assets into production if not thoroughly tested and optimized.
- Ensure supervisors are tasked with minimizing downtime to ensure OEE remains at target levels.
- Establish a routine monthly review to analyse OEE and identify corrective actions required.
Get connected with our sales team
Thanks for your interest in our products and services. Let's collect some information so we can connect you with the right person.