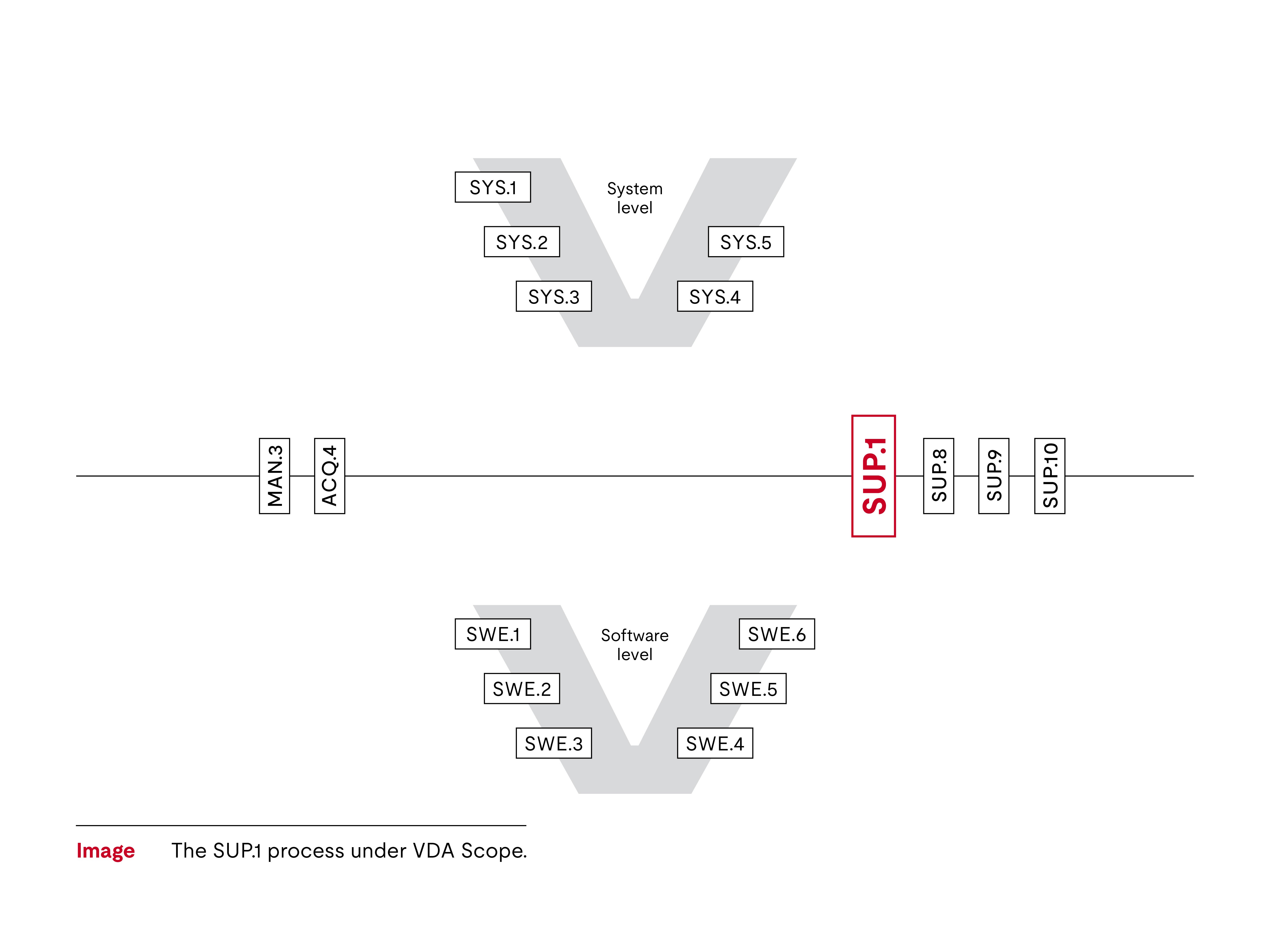
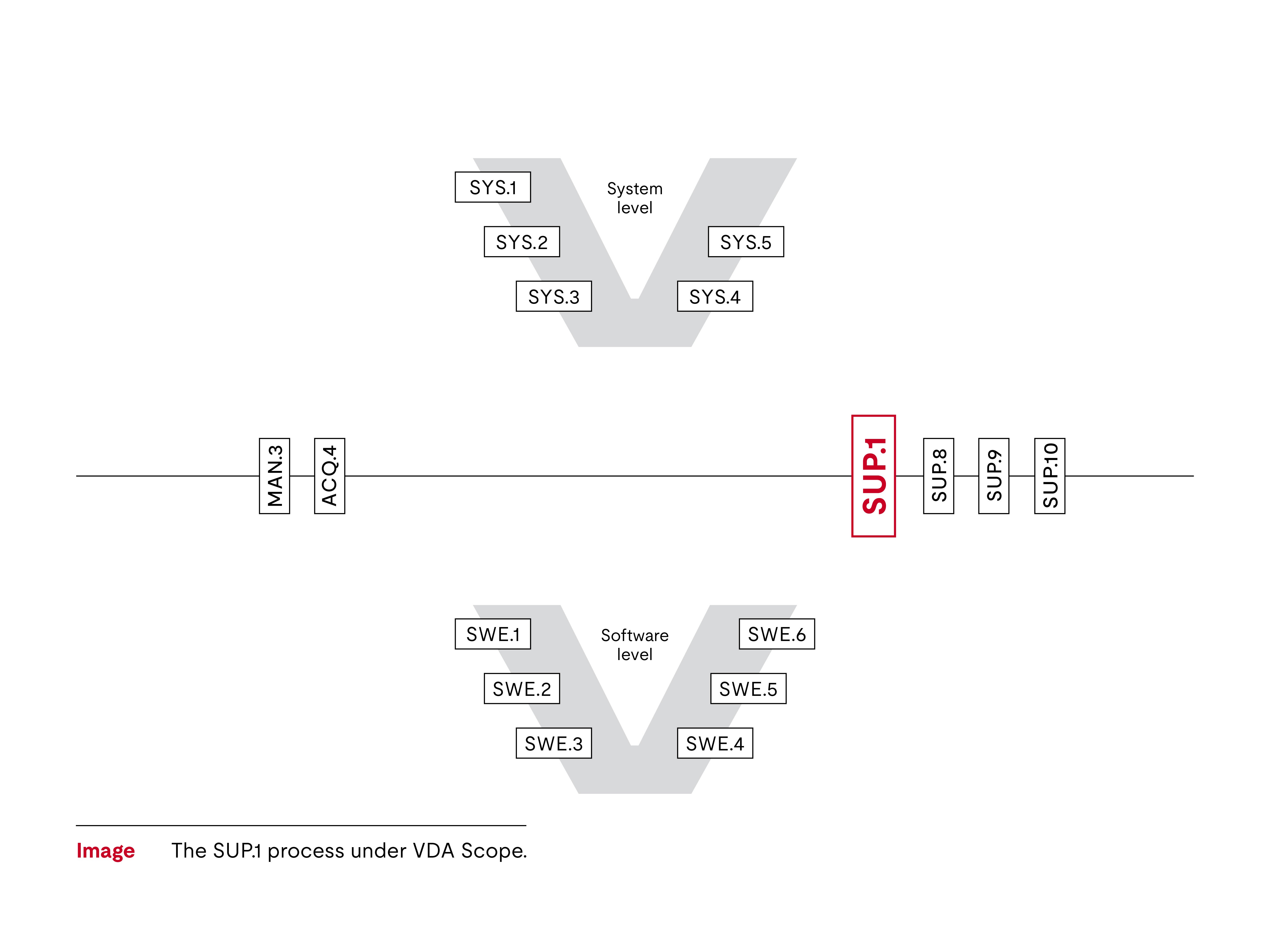
Process ID: SUP.1
Process group: Support
Automotive SPICE® is a trademark of VDA QMC.
The Automotive SPICE® quality assurance process (SUP.1) can help your organization provide independent assurance that quality objectives are met and deviations are resolved.
To do this, independent quality assurance engineers and quality managers work closely with developers. They will establish that corrective action is taken if quality goals are not met. If necessary, they escalate the issue to management through an independent reporting channel and initiate continuous improvement in the project.
This article discusses the most important aspects of quality assurance in Automotive SPICE®.
The most important aspects of quality assurance in Automotive SPICE®
Develop a quality assurance strategy.
An effective quality assurance strategy makes it clear to all involved the quality objectives and how to achieve them. Collect appropriate quality objectives, and align your quality checks with the objectives. This helps companies focus and execute on what is important.
Establish effective quality assurance methods.
Designate an independent quality assurance engineer to support the project. In this context, independent means the quality assurance engineer responsible could stop the project in case of quality problems without fear of any disadvantage to his position from the perspective of the project or from management. The quality assurance engineer helps the project team plan and perform reviews and tests and checks whether the project team is carrying out these activities correctly and on time. Additionally, the quality manager introduces quality issues, methods and tools regarding quality management. Moreover, this person initiates training in quality topics and consults with project team members on quality issues. This position is for process development and for implementing reviews' findings.
Resolve quality problems.
The quality assurance engineer discusses the problem with the responsible person; the quality assurance engineer and responsible person agree on a corrective action and deadline. After the deadline, the quality assurance engineer checks whether the corrective action has been completed. If not, he’ll remind the responsible person, set a new deadline, check again and so on. The quality assurance engineer escalates the issue to the next level of management if someone is not willing to cooperate.
Why choose UL Solutions Software Intensive Systems for Automotive SPICE® support?
As part of our strategy to systematically improve development processes in the automotive electronics sector, UL Solutions Software Intensive Systems is an official licensee of Automotive SPICE®, a trademark of the Association of the German Automotive Industry (VDA QMC).
We can support automotive original equipment manufacturers (OEMs) and suppliers in:
- Achieving the required capability levels within key development processes.
- Systematically improving existing workflows and methods.
- Evaluating the status of process improvements through formal assessments and gap analysis.
- Fulfilling the requirements of Automotive SPICE® in harmony with security, functional safety and agile methods.
- Training staff and assessors.
Read our related content
Automotive SPICE®: Quality assurance - SUP.1 white paper
Services for Automotive SPICE and Extensions
Get connected with our team
Thanks for your interest in our products and services. Let's collect some information so we can connect you with the right person.