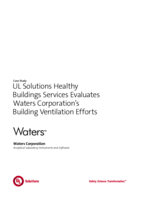
Waters Corp - Indoor Air Quality assessments - Case study
Waters Corp engaged UL Solutions to help oversee and execute a ventilation and indoor air quality testing plan using the ASHRAE 62.1 standard for 16 facilities across 8 countries in 180 days.
For Waters Corporation, a manufacturer of laboratory instruments, chemistries and software for scientists, the global pandemic forced them to quickly determine who among its 7,400 employees worldwide needed to continue working on-site and who could work remotely. The company quickly established an approach to ensure that Waters Corp. could fulfill its public health mandate to support its pharmaceutical and disease research customers during the pandemic.
As a company that manufactures and sells laboratory equipment, the pandemic protocols did more than disrupt human resources, though. Social distancing guidelines limited the number of employees who could work alongside each other in laboratories, on manufacturing floors and loading docks. Following the CDC’s guidelines came with the potential to slow deliveries to customers who relied on the company’s products to research and develop potential COVID-19 vaccines and therapies.
Udit Batra, president and CEO of Waters Corp. wanted to assure its employees that their health and safety concerns were being scientifically and methodically addressed. Batra asked his operations team to collect scientific and quantitative proof that their facilities were safe. To comply with the request, the operations team needed to perform building ventilation tests on the company’s facilities worldwide, a monumental task in the middle of a pandemic.
“We were somewhat caught by surprise,” said Peter Hicks, senior manager of global real estate and a 37-year employee at the company. “We’d already inspected the HVAC systems, intensified our maintenance schedules and started running the HVAC units for extended time periods.
“We had to get started [on proving that the buildings were well-ventilated] very quickly as our CEO wanted people back right away.”
Hicks’ first order of business was to figure out the definition of a properly ventilated building, a seemingly simple task made complex by the company’s global footprint. Historically, ventilation standards vary in both scope and enforcement, e.g., required minimums versus voluntary guidelines. Europe has its own ventilation standards, as does the U.S., China, Brazil, and so forth, which all made determining a baseline for the project challenging.
Additionally, standards often apply differently depending on the type of space and the size of the area under evaluation. With its mix of laboratories, manufacturing plants and sales offices, the assessment formula grew even more complicated for Waters’ real estate and facilities team.
“It wasn’t a case of one building type or the other, but all types,” Hicks said.
Another issue complicating the project was the different cultural approaches to ventilation. In Europe, for example, mechanically ventilating buildings is uncommon, which made it tough for Waters to measure whether a building had proper ventilation.
“Many European buildings have operable windows around the perimeter of an office building,” Hicks said. “Ventilation standards rely on occupants opening windows to bring in fresh air, which is great in the spring and the fall, but not in the winter when windows are barely cracked open.”
Waters Corp. needed a respected third-party organization with an international presence to help solve this critical safety challenge. The company wanted to prove to its employees that it prioritized their health and safety and that the supporting data confirmed the safety of its facilities.
Waters Corp. engaged UL Solutions to help oversee and execute the project. UL Solutions presented the company with a ventilation and indoor air quality testing plan using the ASHRAE 62.1 standard as the project’s foundation.
“UL had that in-house capability for performing both the indoor air quality assessments and the ventilation testing. I can’t imagine that anybody else could have done that.”
With a single starting point for system comparison selected, the team was positioned to launch the project and tested 16 facilities’ ventilation and exhaust systems across eight different countries.
Joel Ritschel, an operations manager in UL Solutions' Asset and Sustainability Performance group, developed a three-pronged approach for the project. First, his team inspected the mechanical and HVAC systems for each building within the project scope.
Next, they measured each system’s air intake which they calculated based on the building’s space usage, square footage and the number of occupants. Then the team compared the measurements to ASHRAE 62.1 to determine whether the ventilation system complied.
Once they completed testing, they developed a report outlining each building’s results along with suggestions on how to improve ventilation outcomes.
The UL Solutions team also performed indoor air quality measurements to determine the air mix within each facility. Dry air commonly consists of various substances, with nitrogen and oxygen making up about 99% of Earth’s atmosphere. Unless adequately ventilated and replenished, indoor air can contain pollutants from colognes, food and even manufacturing substances, along with contaminants such as carbon dioxide, carbon monoxide and formaldehyde. Identifying a building’s air composition allows ventilation system managers to adjust ventilation systems to help meet indoor air quality standards.
Hicks credited the project’s success to their collaborative planning and communication. Waters Corp. and UL Solutions worked closely to coordinate travel schedules, set pre-testing meetings and pre-stage local experts who were familiar with each facility’s ventilation systems.
“One of the things we discovered early on was the importance of pre-planning each site visit,” Hicks said. “UL and I would go over the building plans before arriving on-site, and we held video conference calls with the facilities’ local maintenance teams and UL. This pre-planning helped us move ahead quickly and efficiently without compromising safety.”
UL Solutions also worked closely with Hicks to produce a concise report with pragmatic recommendations for keeping ventilation systems operating correctly.
“Pete and I spent a lot of time on what information we would provide in the report,” Ritschel said. “The reports didn’t have comprehensive technical background information about the project scope or anything extraneous. We put in a user-friendly executive summary and packaged up the information so each site could easily understand the findings and our recommendations.”
“The way we wrote the reports, anybody can read them and understand them,” Hicks added. “UL was able to bring in guys like Joel and Brendan [McCann] who understood HVAC and ventilation systems, the ASHRAE and indoor air quality standards, and how to put all the different pieces together.”
Waters Corp. implemented several other measures to help ensure on-site employee health and safety, including increased facility hygiene, mandatory masking, social distancing, the use of wearable proximity sensors for contact tracing and on-site employee virus testing.
The company’s workplace safety plan relied heavily on tackling airflow in its facilities, given the airborne nature of the novel coronavirus.
“If we didn’t have good ventilation, it would undermine most of our other safety protocols.”
Waters Corp. reported that implementing these crucial elements as a series of safety measures and line of defense helped the company ensure a near-zero rate of on-site COVID-19 transmissions despite more than 300,000 employee visits to essential Waters Corp.’s facilities.
“Ventilation and airflow were key to help us in understanding the safety of our workplace,” Hicks said. “Having the certainty of adequate airflow in our buildings helped us establish and build a framework for our safe return-to-work plans.”
Waters Corp - Indoor Air Quality assessments - Case study
Have questions, need specifics? Let's get this conversation started.