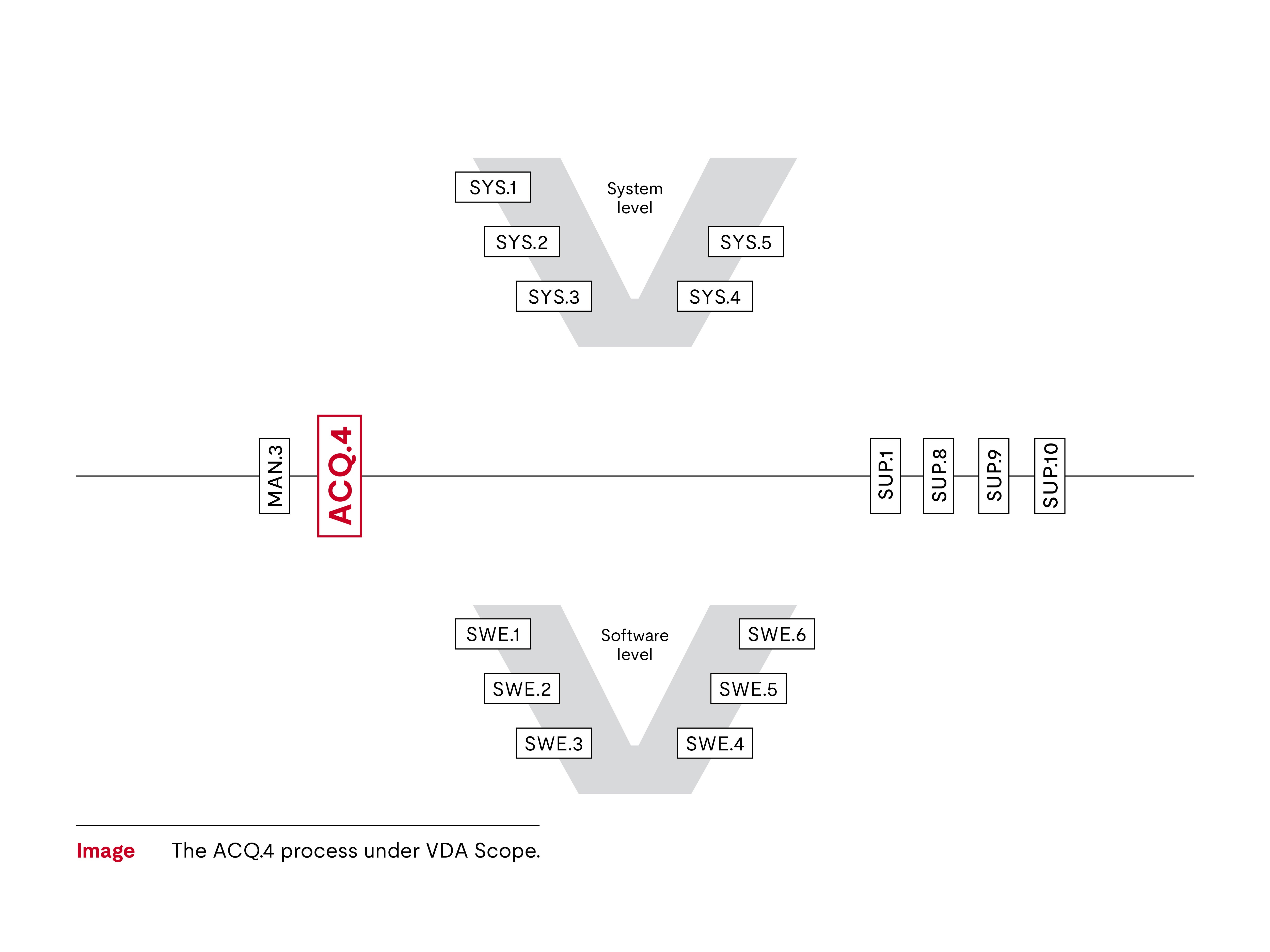
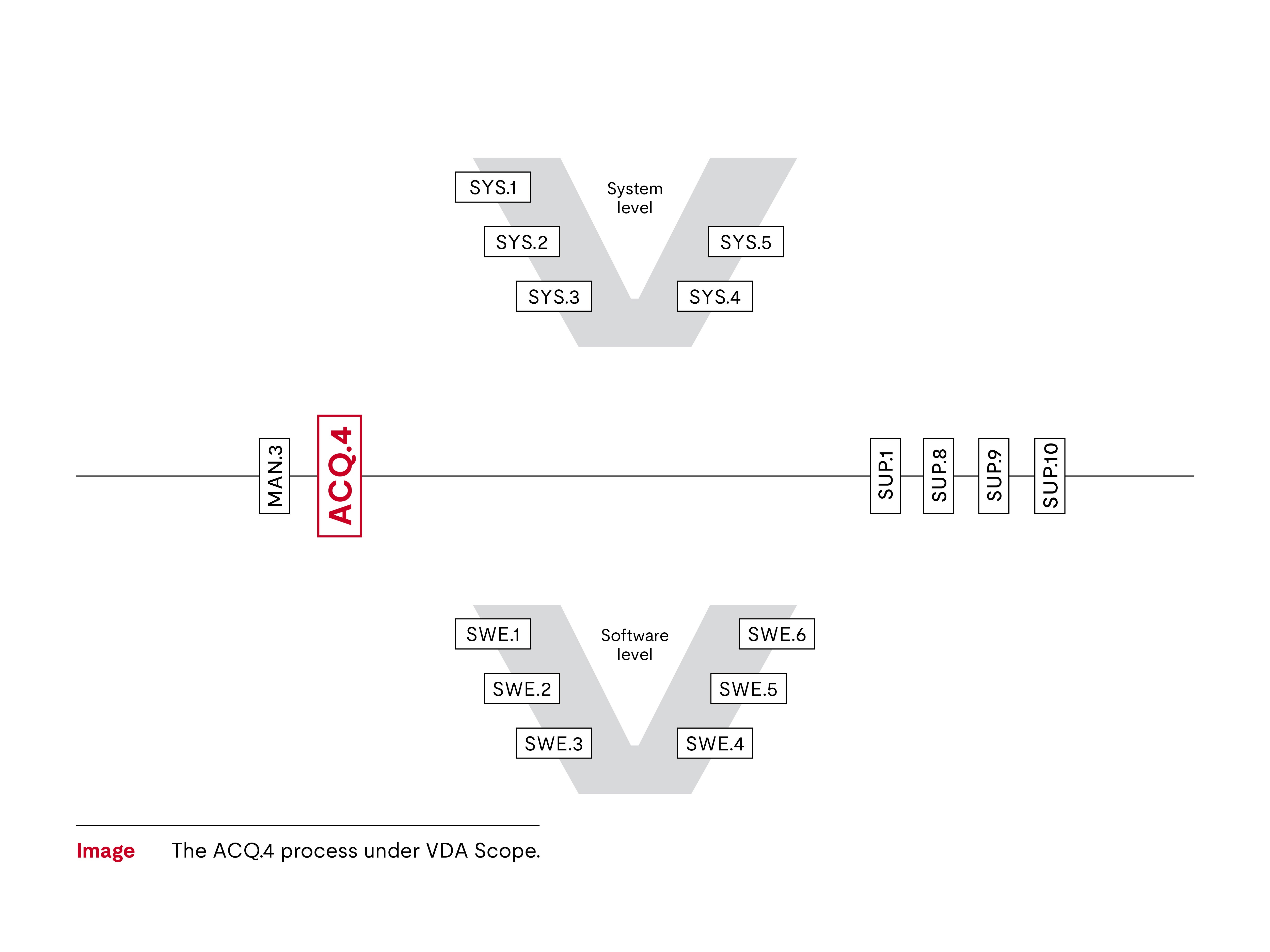
Process ID: ACQ.4
Process group: Procurement
Automotive SPICE® is a trademark of VDA QMC.
The Automotive SPICE® supplier monitoring process (ACQ.4) can help your organization track and assess the performance of the supplier against agreed requirements.
The supplier monitoring process is important because building vehicles involves many complicated supply chains: original equipment manufacturers (OEMs) have suppliers, who in turn have sub-suppliers, who in turn have sub-sub-suppliers. There are many issues that can arise along these chains, such as a subcontractor’s missed deadlines delays the OEM's start of production and subcontractor quality problems that generate high poor quality costs for the OEM.
In the mobility industry and other complex, highly regulated environments, supplier monitoring requires diligent, systematic management at all levels of the supply chain.
In this process, we focus on suppliers who develop a part of our product — typically a software component or a combination of hardware and software, such as a sensor. The component should be developed according to our specification, and this requires considerable management effort. In contrast, the purchase of commercial-off-the-shelf (COTS) products does not require the same level of management.
Keep reading to discover the most important aspects of supplier monitoring in Automotive SPICE®.
Define the way of cooperation
A kick-off workshop typically is organized between the two parties at the beginning of a project. Both sides give a commitment to carry out the agreed-upon tasks. Establish a written agreement, usually called Supplier Statement of Work, that defines aspects, including interfaces, responsibilities, meetings, joint activities, common processes, reporting, timeline and milestones.
Particularly important questions to consider when forming this agreement include the following:
- What are your requirements for the supplier development process? In particular, what Automotive SPICE® requirements do you request from the supplier? Are there any other norms or standards for safety, security, etc., that need to be considered?
- When and in what format will you provide the supplier with your requirements?
- What is your process for the supplier’s review and acceptance of requirements?
- How do you deal with conflicts if the supplier does not accept requirements?
- What tests are performed after the supplier has implemented the requirements?
- Which tests are carried out by the supplier and which are carried out by you as customer?
- What support do you expect from the supplier after the tests are completed so that their product works in your environment?
Additional topics to consider include reporting, escalation mechanisms, risk management, technical documentation and regular meetings.
Provide appropriate resources to manage the supplier
It is a common mistake to severely underestimate the capabilities required to manage a supplier. An experienced person must invest a reasonable amount of time to manage the supplier. In large companies, someone may be dedicated to dealing with the supplier on a full-time, daily basis. For offshore suppliers with cultural and language barriers, the effort can be much greater than working with a local supplier. In some cases, supplier managers dealing with offshore suppliers implement short, incremental development cycles. For example, on the first day, they discuss requirements. On the third day, they check the software delivery and determine deviations from the requirements, and on the fourth day, they begin the process again. The Automotive SPICE® Project Management (MAN.3) establishes an organization chart and a process to monitor resources.
Establish effective means of monitoring suppliers’ progress
There are many methods to monitoring suppliers’ progress, including:
- Hold a technical meeting to discuss and clarify requirements, technical questions, problems and quality issues. Maintain a list of unresolved items, and manage the items until they have been resolved.
- Check progress against the schedule, check effort and costs (if it is a time and material contract), and handle change requests, forecasts and risks.
Why choose UL Solutions Software Intensive Systems for Automotive SPICE® support?
As part of our goal to systematically improve development processes in the automotive electronics sector, UL Solutions Software Intensive Systems is an official licensee of Automotive SPICE®.
We can support automotive original equipment manufacturers (OEMs) and suppliers in:
- Achieving the required capability levels within key development processes.
- Systematically improving existing workflows and methods.
- Evaluating the status of process improvements through formal assessments and gap analysis.
- Fulfilling the requirements of Automotive SPICE® in harmony with security, functional safety and agile methods.
- Training staff and certified, qualified assessors.
Read our related content
Supplier Monitoring – ACQ.4 in Automotive SPICE® white paper
Services for Automotive SPICE and Extensions
Get connected with our team
Thanks for your interest in our products and services. Let's collect some information so we can connect you with the right person.