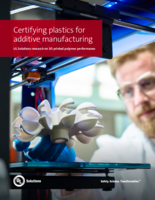
Certifying plastics for additive manufacturing
As a global safety science leader, UL Solutions helps companies to demonstrate safety, enhance sustainability, strengthen security, deliver quality, manage risk and achieve regulatory compliance.
See how we put safety science to work to help create a safer, more secure and sustainable world for you.
Explore our business intelligence-building digital tools and databases, search for help, review our business information, or share your concerns and questions.
Accelerate your planning process and learn the requirements needed to take your products to market worldwide.
A secure, online source for increased visibility into your UL Solutions project files, product information, documents, samples and services.
Access UL certification data on products, components and systems, identify alternatives and view guide information with Product iQ.
ULTRUS™ helps companies work smarter and win more with powerful software to manage regulatory, supply chain and sustainability challenges.
Discover the importance of certifying and using plastics materials that are appropriate for use in 3D printing.
3D printing – or additive manufacturing (AM) – offers unprecedented versatility to manufacture complex parts and products directly from digital files. Printing parameters can be changed during the process, tailoring material properties to perfectly fit any given portion of a printed product. This incredible versatility, however, introduces a new level of complexity not seen in conventional manufacturing.
In the AM industry, the mechanical properties of a material, such as tensile and impact strength, will vary considerably more when 3D printed than molded by conventional methods, such as injection molding. Less commonly understood, however, is that 3D printing may influence a material’s safety-critical performance properties, such as ignition, flammability and dielectric strength.
UL’s plastics experts conducted a systematic research study to fill in the knowledge gap. This white paper provides a summary of their findings.
Certifying plastics for additive manufacturing
To access the white paper, “Certifying Plastics for Additive Manufacturing,” please fill out the form below: